Factors affecting heat sink extrusion profiles
Heat sink extrusion profiles need to have good thermal conductivity. The most widely used aluminum profiles are 6061 and 6063. 6063 has good thermal conductivity and good mechanical properties. Therefore, 6063 is most widely used. The following factors need to be considered if the radiator aluminum profile is of good quality:
Aluminum bar quality for heat sink extrusion profiles
The alloy composition of the aluminum bar should be strictly controlled to ensure a sufficiently homogeneous mixture to ensure the uniformity of the organization and properties. The surface of the aluminum bar must be smooth and should be free from segregation and sand. In addition, the end of the aluminum bar should be flat, not cut into steps.
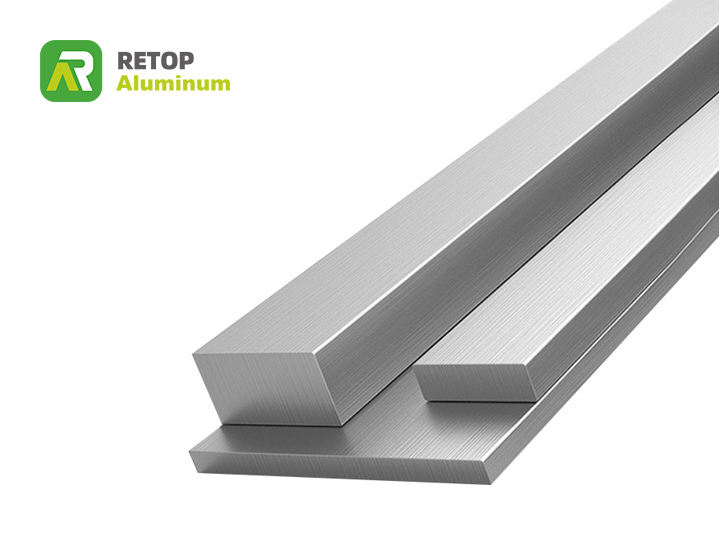
Reliable molds for making aluminium heat sink
Because aluminum heat sink extrusion profiles have many radial shaped aluminum sheets. During the extrusion process these pieces are subjected to a lot of pressure. At the same time each aluminum piece must be very tough. So the quality of the tool steel must be reliable. Generally H13 tool steel is used.
Aluminium heatsink extrusion profiles mold heat treatment
In order to ensure that all parts of the die are quenched uniformly, it is recommended to use vacuum heating for quenching, or high pressure pure nitrogen quenching for better results. This process should include three tempering, in order to maintain the hardness of the mold in the HRC48 ~ 52 at the same time to ensure sufficient toughness. This step is very important to prevent the mold from fracturing.
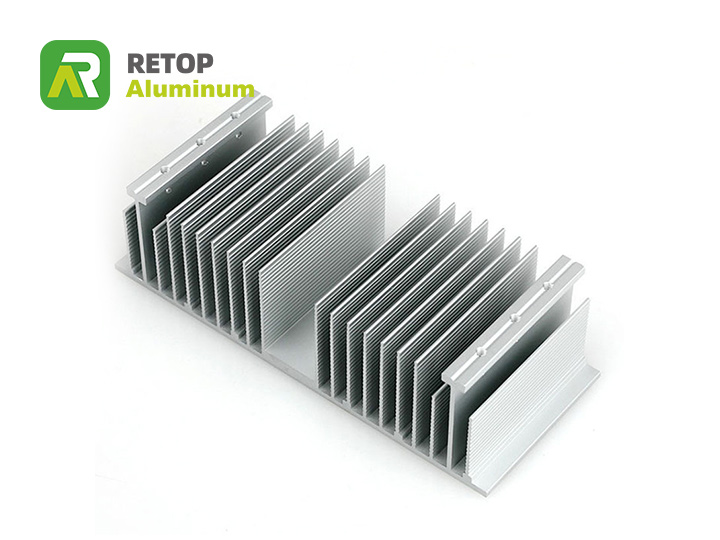
Reduce extrusion pressure
To avoid fin breakage, efforts should be made to reduce the extrusion pressure. Extrusion pressure is affected by the length of the aluminum bar, the resistance of the alloy to deformation, and the degree of deformation. Therefore, it is recommended that the length of the aluminum bar should not be too long, usually about 0.6 to 0.85 times the normal length.
For complex shaped aluminum heat sink sections. First, consider shortening the length of the cast bar, and then use a pure aluminum short cast bar for the initial extrusion test. After the success of the initial extrusion, extrusion production is then carried out using ordinary cast rods.
By subjecting aluminum bars to a uniform heat treatment, not only is it possible to achieve a uniform distribution of microstructure and properties, but it also helps to improve extrusion performance and reduce the pressure required for extrusion. Therefore, aluminum bars need to be uniformly heat-treated.
Extrusion heat sink extrusion profiles process
The key to the production of aluminum heat-sink profiles lies in the initial testing of the extrusion die. The operator should advance the main plunger gradually at a low pressure of less than 8 MPa to ensure that each fin is extruded evenly. After that, the pressure can be gradually increased to increase the extrusion speed. During the extrusion process, care must be taken to control the heating temperature of the die to ensure that the die temperature is close to the cast bar temperature.
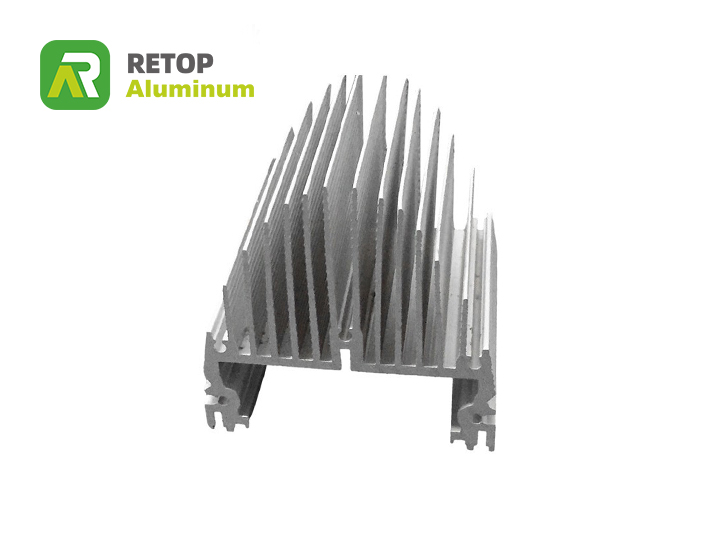